A static approach to serving relevant knowledge at the right time
We already discussed how to use mathematics to organize our expert knowledge about error codes and problem areas in a knowledge model of causes, actions, and questions using probabilities, time, and cost and troubleshooting like the best. However, dynamically calculated troubleshooting guides are not the best construct for all types of knowledge. When it comes to performing static procedures like assembly, commissioning, service, component replacements, assessments, test, billing, HR, and other well-known workflows that just requires us to get from A to B, we need another model for knowledge – a static approach to serving relevant knowledge at the right time.
The importance of correct equipment assembly
Assembling complex machinery like wind turbines, trucks and excavators can run in the 100s or even 1000s of hours on-site (we have seen examples of huge mining excavators taking as much as 6.000 hours to assemble and commission fully). It involves advanced and expensive special equipment, many shipments with parts, a team of skilled engineers, and a huge amount of documentation describing each and every detail.
It is absolutely necessary that the field service team on-site performs the assembly and commissioning properly and follows the instructions carefully, not skipping steps and ensuring that instructions are carried out in the correct order.
Consider the example below – replacing a front wheel hub on a mining excavator. The purple boxes lead to other instructions with more flows totaling around 100 steps, each explained by elaborate text, images, and videos.
The importance of assembling and testing machines correctly before commissioning is huge as machines that are incorrectly built will break faster than properly assembled and commissioned machines. Most machines simply stays longer in operation before seeing issues if they are done right from the start.
If assembly instructions are provided as traditional endless pages of static documents with 100’s of work instructions for assembling complex machines, important steps will inevitably get missed or performed incorrectly.
Add to that geographically diverse teams and varying skill levels of the engineers involved – no guarantee that the products are assembled, calibrated and tested correctly every single time eventually leading to errors and sub-optimal equipment performance. Start-up procedures must be followed by all teams every single time a new machine is installed and assumes operation – ensuring optimal performance, improved reliability, less errors, smooth operations and happy customers!
Correct assembly and the P-F curve
Within maintenance and reliability, the P-F curve (Point of defect and point of Functional failure vs. time) is used to demonstrate the relationship between machine breakdown, cost, and how to prevent it. Just because a machine is in operation and working now doesn’t mean that it doesn’t contain errors or defects that are already beginning to occur within the machine. As soon as a new machine has gone through start-up procedures and becomes operational, wear and tear start happening, and eventually, failures will occur – the potential defects start to move down the P-F curve until the failure happens.
The curve illustrates how a potential failure becomes increasingly more expensive to fix the longer it goes unhandled – and as such, it is an essential tool for understanding the effects of proactive and condition-based maintenance.
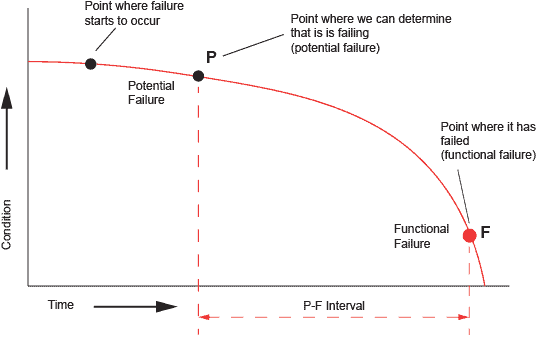
However, if the machine contains defects, errors, and other potential failures before it has been in operation a single hour, the machine starts the move down the P-F curve way too soon, and the cost of repair begins to increase.
Had an important lubrication step been missed, that particular component is bound to fail very soon but had the instructions been clear and the lubrication performed properly, the component would have been operating correctly for a long time.
Correct assembly and commissioning of new products is actually a very proactive way of ensuring a smooth and failure-free operation for as long as possible. It prolongs the time the machine can operate before starting the move down the P-F curve.
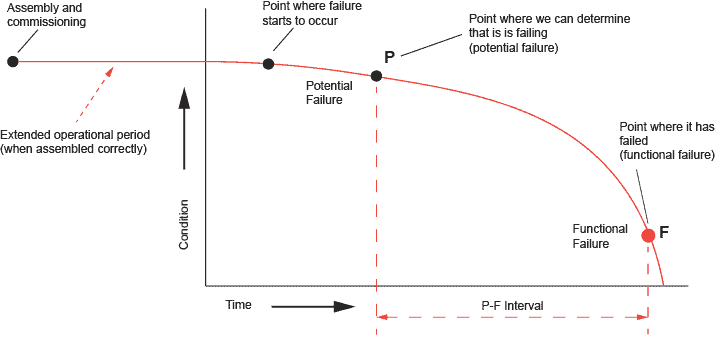
Our experience shows that being served assembly instructions in small manageable pieces of content one step at a time is far superior to long-form static documents as it is easy to get lost in long documents increasing the chance of missing important information along the way. Furthermore, the step-by-step approach provides a great opportunity to track what the assembly teams have actually performed as well as the time spent performing each step – important data in the quality assurance process where it helps identify problematic time-consuming steps in complex procedures.
Next, we will look into how we capture knowledge and especially elicit all the tacit knowledge we typically have within enterprises.
About us
We have 20 years of experience in helping businesses of all sizes capturing, organize, and optimize expert knowledge. We work with clients in industries ranging from wind, mining, and electronics to consumer printing and telecommunications.
Get in touch and see why they trust Dezide to build brilliant knowledge bases powering the world’s best service organizations.